1960s pop icon Marianne Faithfull has died at her home in London
Supply chains are breaking. They’ll rebuild stronger.
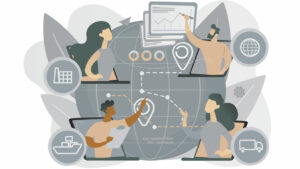
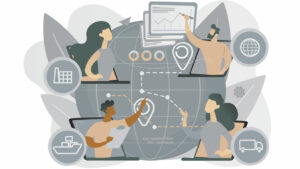
PICK a single item from an array of shocks and you can see just how fragile global supply chains truly are. But combine climate change, decoupling from China, unprecedented technological development, wars, rising costs and labor shortages, and we now have an amalgam of catalysts that will change global trade for the better.
The pandemic is seen as the primary cause for many of the disruptions over the past four years. A halt to flights, factory shutdowns in China, and surges in demand for specific products broke supply chains. Yet the weaknesses were already there, hidden by an often-improvised interplay between manufacturers, shippers, logistics providers, and retailers.
What COVID taught us, though, is that just-in-time inventory strategies — keeping only what’s immediately needed — aren’t robust enough to handle deviations from the norm. Ironically, Toyota Motor Corp., an early pioneer of keeping low stockpiles, quietly ditched this lean approach around a decade ago. As a result, the Japanese carmaker sailed through the chip shortage relatively unscathed, while rivals General Motors Co. and Ford Motor Co. tweaked their products and halted factory lines to adjust to a lack of parts.
The tech sector went through a similar rethink. Apple, Inc. is the standard bearer, while Taiwan Semiconductor Manufacturing Co. (TSMC) and Foxconn Technology Group are prime examples of supply-chain providers that made adjustments long before they were needed. The process of making an iPhone starts upstream with TSMC providing chips, then Foxconn assembling the devices before Apple handles logistics and sales. Over the past decade, each of the upper, middle, and downstream links in the supply chain have almost doubled the proportion of inventory they hold.
This expansion of reserves across sectors from cars to cellphones has ameliorated the impact of one-time shocks such as COVID shutdowns, labor shortages, and war. Yet recent events have proven that stockpiles alone aren’t enough to shepherd us through crises.
The modern global economy relies on Adam Smith’s free-market belief that countries should focus on what they’re relatively better at, rather than erecting protectionist barriers and trying to make everything locally. Smith’s thesis was found within his revelatory opus An Inquiry Into the Nature and Causes of the Wealth of Nations — the late 20th century’s embrace of trade liberalization did indeed bring wealth to many nations and lifted billions of people out of poverty.
The result was a hub-and-spoke structure for global production, with China at the center. That model gained momentum after the Soviet Union fell and the world enjoyed relative peace — but it was only possible because of a rapidly expanding network of global aviation and marine transport. Huge aircraft and even bigger ships meant it was quicker and cheaper to make everything in one place, then transport it across the globe rather than attempt local production closer to the end market. Smith was right, it seemed.
An almost total cessation of passenger flights from the start of the pandemic in 2020 was the first sign that this model is too brittle. The closure of the Suez Canal, caused by poor piloting in the waterway, in 2021 was a stark reminder of how unstable one single stretch of marine traffic can be. The blockage also highlighted how much we rely on just a few supply lines to connect major consumption economies to a handful of production bases. On the other side of the world, climate change is creating drought and slowing traffic through the Panama Canal that joins Asia to eastern America.
Growing suspicion between the US and China may be the saving grace.
International buyers have long known that it was risky to put all their production eggs in one basket. But heightened tensions, including a Tech Cold War, have forced clients and suppliers to shift away from China to India, Vietnam, and Mexico. None will replace the former, but over the coming years, we should expect a shrinking proportion of products to be sourced from the world’s second-largest economy.
India, now the most populous nation, will take some of that business, but the days of mega factories — as seen in China’s Shenzhen and Zhengzhou cities — is over.
Logistics providers will need to adjust, too. Journeys from ports such as Shanghai to US destinations like Los Angeles were once the busiest routes in maritime transport. That allowed shipping companies to pile over 20,000 containers onto a single vessel, bringing unprecedented economies of scale. This benefit has faded over the past few years because China is no longer a source of cheap labor — indeed, it is often in shortage.
Now intra-Asian routes, which connect nations such as Cambodia, the Philippines, and Vietnam, are the busiest. A lot of this traffic is simply shifting half-finished goods to the next factory in the manufacturing chain, while some of it is recognition that Asian countries are now major consumers of global output.
This diversification of transport to smaller ports in the region will force lighter cargoes to be carried on lesser ships. As a result, the global industry must contend with a supply chain that consists of more docks connecting a larger number of factories, each processing fewer goods.
The crises that have brought supply chains to their breaking point have highlighted an urgent need for change. This will result in a far more robust and balanced framework for global trade and manufacturing.
BLOOMBERG OPINION